Related Items
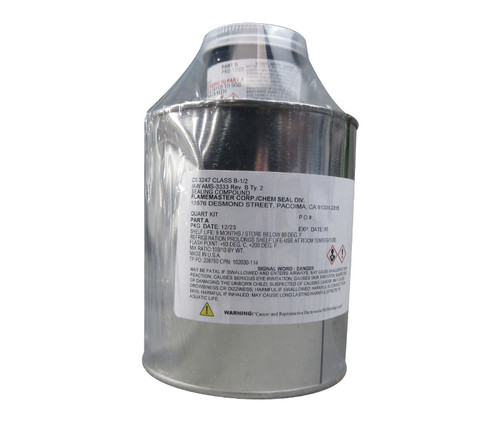
Flamemaster CS-3247 B-1/2 Black AMS-3333B Type 2 (no QPL) Spec Canopy & Windshield Sealant - Quart (24 fl oz) Can Kit
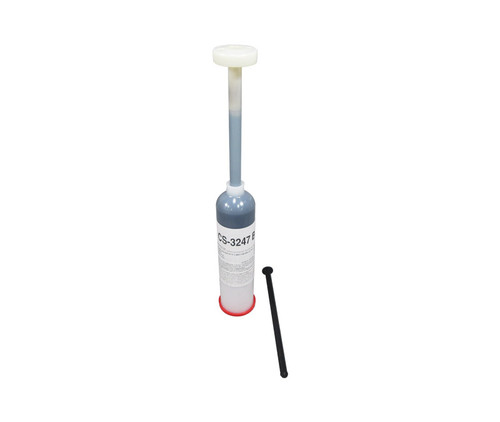
Flamemaster CS 3247 B-2 Black AMS-3333B Type 2 (no QPL) Spec Canopy & Windshield Sealant - 6 oz (3.5 fl oz) Tube
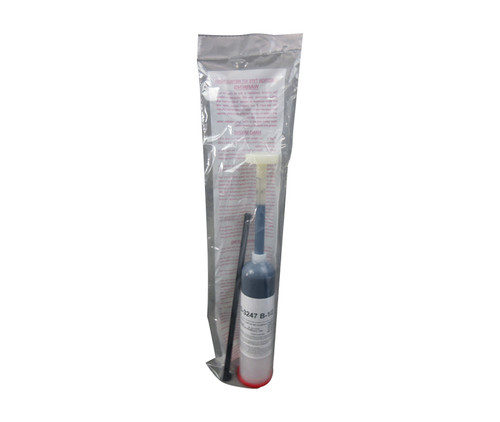
Flamemaster CS 3247 B-1/2 Black AMS-3333B Type 2 (no QPL) Spec Canopy & Windshield Sealant - 6 oz (3.5 fl oz) Tube
Approvals and Conformities
Product Attributes

Features
ApplicationPropertiesPerformanceProperties | |||
Application | Properties | Performance | Properties |
Color | Color (Mixed) | Black | |
Base Compound | Black | Specific Gravity | 1.63 |
Accelerator | Black | Thermal Rupture | >10psi at 250F |
Mixing Ratio | PartA/Part B | Hardness Shore A | 45-50 |
By Weight | 100:10 | Low Temperature Flex | -65F |
Nonvolatile (mixed) | 97% | ||
Viscosity Brookfield | 14,000 poises | Adhesion (Peel) | 100% Cohesive |
Vertical Flow (slump) | <0.25 | 7 day cure at 75F | After weathering |
Stress Crazing | Aluminum: 35 lb/in | ||
Polycarbonate | Non-crazing | Stainless: 30 lb/in | |
Acrylic | Non-crazing | Titanium: 30 lb/in | |
Corrosion | Passes | Polycarbonate: 37 lb/in | Polycarbonate: 40 lb/in |
Fuel resistance | passes | Acrylic: 35 lb/in | Acrylic: 38 lb/in |
Glass: 35 lb/in | |||
Application Time | Tack Free Time | Cure to 35 Shore A | |
B-1/2 | 1/2 hour >15 gm | 8 hours | 30 hours |
B-2 | 2 hours > 15 gm | 24 hours | 48 hours |
SURFACE PREPARATION
To obtain good adhesion the surfaces must be dry and free of all traces of oil, wax, grease, dirt or other contamination. The solvent blend selected should address the contamination present on the substrate to receive the sealing compound. The solvent blend should not adversely effect the substrate to be cleaned The solvent blend should not leave a residue on the surface to which the sealing compound is to be applied.MIXING INSTRUCTIONS
Prior to the mixing of any sealant material the user should refer to the Material Safety Data Sheet supplied by the manufacturer. Safety glasses should be worn at all times when mixing or dispensing sealants CS-3247 Parts A and B are carefully matched at time of manufacture to provide optimum performance during application and when cured. The container labels identify which Part A to use with which Part B.When material is supplied in 50 gallon drums or 5 gallon pails to be utilized with a Graco Hydra-mate (or equal) proportioning and dispensing machine the mix -ratio by volume is 8.3 parts curing compound to 100 parts of the base compound. Prior to placing the curing agent pail on the dispensing equipment the curing agent should be stirred. The dispensing equipment manufacturer's recommendations for correct operation of the equipment should be followed.
When material is to be hand mixed a ratio (by weight) of 10 parts curing compound to 100 parts of the base compound is used. The material should be mixed in a clean container alternately scraping down the sides to insure dispersion of the curing agent, mix until a uniform color is obtained. As both part A and Part B are Black, thorough mixing should be employed to insure adequate dispersal of the curing compound. The part B curing compound should be stirred before weighing out the necessary amount.When the material is supplied in two component sectional plastic kits; the instructions printed on the kit package should be followed, instructions are provided for both manual and machine mixing.