Related Items
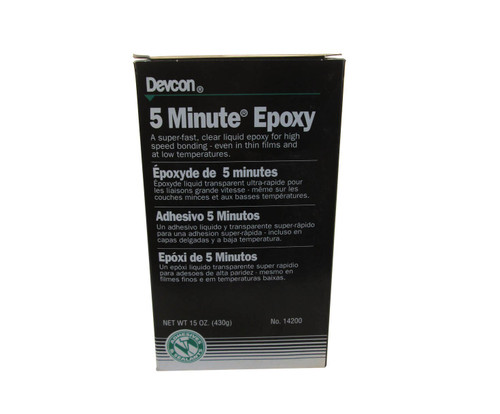
Devcon® 14200 5 Minute® Epoxy Rapid-Cure General-Purpose Adhesive - 15 oz Kit
PART #:
SGP16072
MFR PART #:
14200
Regular Price:
Our Price:
Our Price:
Sale Price:
$92.98
Adding to cart… The item has been added
Adding to cart… The item has been added
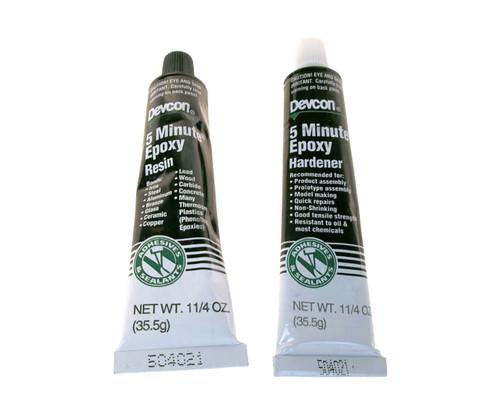
Devcon® 14210 5 Minute® Epoxy Rapid-Cure General-Purpose Adhesive - 2.5 oz Tube
PART #:
SGP16074
MFR PART #:
14210
Regular Price:
Our Price:
Our Price:
Sale Price:
$17.90
Adding to cart… The item has been added
Adding to cart… The item has been added
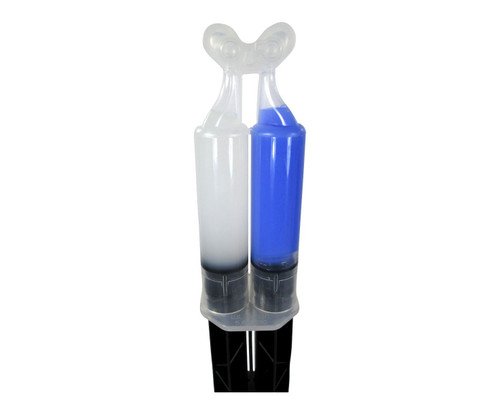
Devcon® 14240 5 Minute® Epoxy Rapid-Cure General-Purpose Adhesive - 25 mL Dual Syringe Tube
PART #:
SGP16087
MFR PART #:
14240
Regular Price:
Our Price:
Our Price:
Sale Price:
$14.77
Adding to cart… The item has been added
Adding to cart… The item has been added
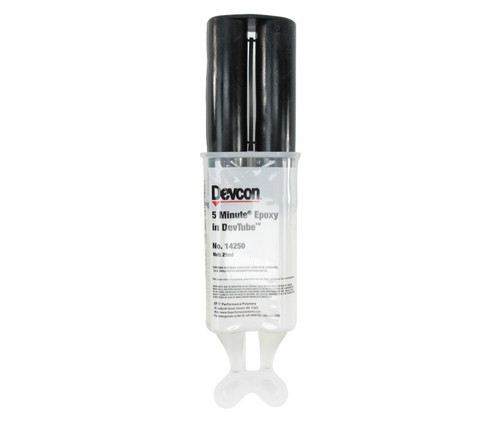
Devcon® 14250 5 Minute® Epoxy Rapid-Cure General-Purpose Adhesive - 25 mL Dev-Tube™
PART #:
SGP16090
MFR PART #:
14250
Regular Price:
Our Price:
Our Price:
Sale Price:
$12.84
Adding to cart… The item has been added
Adding to cart… The item has been added
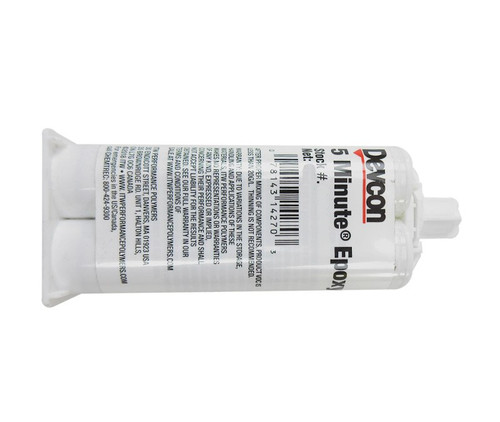
Devcon® 14270 5 Minute® Epoxy Rapid-Cure General-Purpose Adhesive - 50 mL Mark 5 (Dev-Pak)
PART #:
SGP195374
MFR PART #:
14270
Regular Price:
Our Price:
Our Price:
Sale Price:
$24.74
Adding to cart… The item has been added
Adding to cart… The item has been added
Approvals and Conformities
NSN
8040-01-667-0270
Hartzell PN/Spec#
A-6741-215
Product Attributes

United States
Size
25 mL
Shipping Weight
0.2 pounds
ECCN
EAR99
Color Family
Clear
Manufacturer P/N
14240
Schedule B Code
1301.90.0190
Pack Quantity
1
Ship Dimensions
7 x 2 x 2 inches
Size
25 mL Dual Syringe Tube
Color
Clear
Fast-curing, thixotropic, non-migrating adhesive designed for filling gaps and bonding rough or smooth surfaces, including metal, ceramic and wood. Disappearing blue coloring tells you when the product is thrououghly mixed for easy use!High tensile strength (2,500 psi) Fills gaps to .250 inches Good solvent resistance to gas, oil and other solvents Non sag makes it ideal for use on vertical surfaces Excellent gap filling qualities without tremendous shrinkage Fast curing for bond tags on machinery and equipment