Related Items
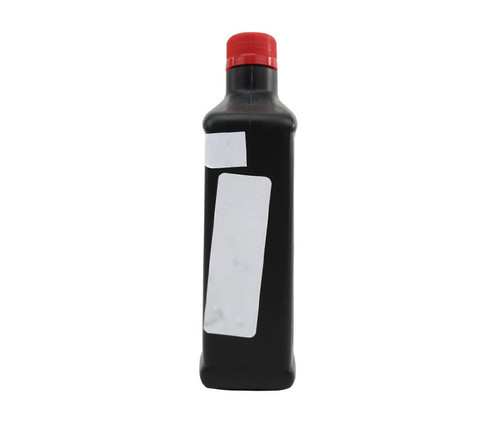
CamGuard™ Aviation Engine Oil Supplement - 16 oz Bottle
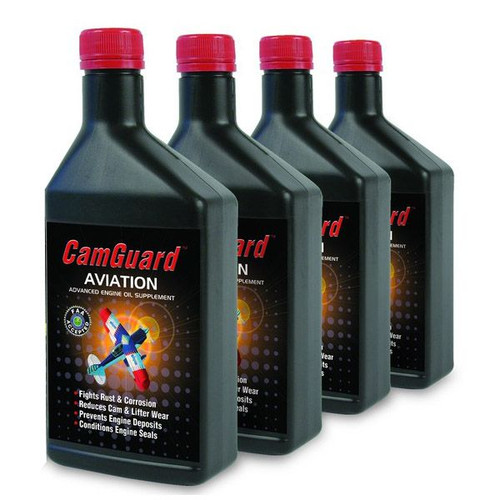
CamGuard™ Aviation Engine Oil Supplement - 4 Bottle/Pack
Approvals and Conformities
Product Attributes

Buy a 4-pack for savings here
CamGuard™ is an additive package formulated to address the complex and interrelated problems of corrosion, wear, deposits and seal degradation in piston engines. It is compatible with and designed to improve the performance of all oils including mineral based, semi-synthetic and fully synthetic types. CamGuard™ is especially useful for infrequently used engines including aircraft, marine, motorcycles, emergency equipment, backup generators, classic and antique vehicles, agricultural and all seasonal equipment.
CamGuard™ contains 11 multifunctional components. Each of these components has a primary function and at least one secondary function. This is how CamGuard™ achieves superior performance with the addition of only 5 volume percent.
Features
ASL CamGuard Corrosion Testing of Aviation Oils
Aircraft Specialties Lubricants performed additional corrosion testing using the latest humidity cabinet testing procedure, DIN 50017. This is a worldwide reference test procedure showing both greater repeatability, test to test, and greater reproducibility, lab to lab, than the ASTM 1748.
Tested were 20W-50 semi-synthetic (SS), 15W-50 semi-synthetic (SS), 20W-50 AD, W100 AD and W100 storage oil. Both semi-synthetic oils and the storage oil have corrosion inhibitor packages.
This test is cyclic and uses distilled water. One cycle is 24 hours (1 day) and consists of 8 hours at 100% relative humidity (condensing) at a temperature of 122°F followed by 16 hours at ambient humidity at a temperature of 75°F. Matte finish sandblasted, SAE 1010 mild steel panels were used for this testing. The panels were dipped in the oils and then allowed to drip/drain for 2 hours.
Figure 1 shows the average number of days to the appearance of significant rust on the panels. All of the oils show a remarkable improvement with the addition of CamGuard. Moreover, all of the samples with CamGuard showed an impressive improvement over the long-term storage oil.
ASL CamGuard Derived Humidity Cabinet Testing
Aircraft Specialties Lubricants performed corrosion testing on four oils and three additives based on the American Petroleum Institute (API) methods for automotive oils. We used a cyclic humidity chamber and matte finish SAE 1010 low carbon mild steel test panels. The water in the chamber was mildly acidified with hydrochloric acid.
The oils tested were AS W100 Plus, AS 15W-50 semi-synthetic (SS), P 20W-50,EX 20W-50 semi-synthetic (SS). The additive were tested as follows: Additive A 6% in AS W100 Plus, Additive B ྪ%) in AS W100 Plus, CamGuard 5% in AS W100 Plus, CamGuard 5% in P 20W-50.
The panels were dipped at ambient temperature 75 ° F. and allowed to drain for 30 minutes. They were then suspended in an oven at 220 ° F. for 30 minutes where they continued to drain/drip. This was done to simulate engine shutdown.
The samples were placed into the humidity cabinet. The temperature in the cabinet cycled between 65 ° F.and 100 ° F. every 24 hours. This cycled the samples around the dew point demonstrated by condensation onthe panels. We checked the samples once per day for corrosion.
The crankcase of an airplane engine is an aggressive environment. Blow-by contains partially combusted and raw fuel components, combustion gasses, and water. These contaminants lead to a hostile acidic environment promoting corrosive/erosive wear that can dramatically reduce engine life. Hydrochloric* acid was used to simulate the acidic/corrosive environment of the crankcase and to increase the severity of the tests. We terminated the testing at 60 days for the CamGuard samples more than tripling the protection time of the best oil. See Figure 1.
*Hydrochloric acid was selected because of its use in the standardized ASTM testing protocol for certifying automotive engine oils. The Ball Rust Test (BRT) is currently utilized to qualify passenger car motor oils for ferrous metal corrosion protection. It exposes a polished steel sample ball, in the test oil, to a mixture of hydrochloric, hydrobromic, acetic acid, water and air.
RUST PROTECTION
Figure 2.
ASL CamGuard Inclined Panel Deposit Test
15W-50 Semi-synthetic oil
With and Without CamGuard
540ºF – 2 hours
With CamGuard | Without CamGuard |
540ºF – 4 hours
With CamGuard | Without CamGuard |
The Inclined Panel Deposit test is used to determine how well a lubricant resists oxidation and deposit formation due to thermal breakdown. The stainless steel panels are held at an incline at a temperature of 540 degrees F. Oil is dripped continuously along the centerline of the panel one quarter of the way down marked by the two lines. The oil flows toward the pointed end of the panel where it drips off to be collected and reapplied to the hot panel. This accelerated test is designed to emulate the deposit forming tendencies of oils.
Aircraft engines are designed to run with large clearances. The reasons for this include the age of their design, the materials used, and most importantly the fact that they are air-cooled. Large clearances between pistons and cylinders lead to large amounts of blow-by, the gas that leaks by the piston rings during the high-pressure combustion events. Blow-by gas is made up of combustion by-products such as carbon dioxide, water and lead oxides, it also contains large amounts of air, partially combusted fuel (very reactive) and raw fuel. An engine that uses 15 gallons of fuel per hour may put 0.5 gallons of partially combusted and raw fuel into the crankcase per hour. Most of these fuel components are volatile and the vapors exit the engine through the crankcase breather. Other components are less volatile and remain in the engine diluting the oil. It is the blow-by gas that contaminates the oil and gives it that characteristic smell after only a few hours. It is the blow-by components that remain in the oil that are real troublemakers. They not only dilute the oil and additives but they are extremely reactive. In the upper ring zone they overwhelm the dispersant and antioxidants leading to carbon and lead deposits. Analysis of deposits found in the upper piston ring groove show them to contain over 2% lead and therefore fuel derived. Oil companies only put enough antioxidant to protect the bulk oil from oxidizing. This however is not the problem. CamGuard uses multiple high molecular weight antioxidants to address this “blow-by fuel dilution” unique to aircraft engines. The result is fewer deposits, which dramatically reduces the chance of sticking piston rings or valve guide “morning sickness”.
Aircraft Specialties Lubricants tested a popular 15W-50 semi-synthetic oil with and without the addition of 5% CamGuard. The results on both the 2 and 4 hour tests show a dramatic reduction in the total amount of deposit formed with the use of CamGuard.
ASL CamGuard High Pressure Differential Scanning Calorimetry Test
Aircraft engines are designed to run with large clearances. The reasons for this include the age of their design, the materials used, and most importantly the fact that they are air-cooled. Large clearances between pistons and cylinders lead to large amounts of blow-by, the gas that leaks by the piston rings during the high-pressure combustion events. Blow-by gas is made up of combustion by-products such as carbon dioxide and water. It is also the source of lead found in the oil. It also contains partially combusted fuel (very reactive) and raw fuel. An engine that uses 15 gallons of fuel per hour may put 0.5 gallons of partially combusted and raw fuel into the crankcase per hour. This highly reactive mixture chews up the additives in the oil. Most of these fuel components are volatile and the vapors exit the engine through the crankcase breather. Other components are less volatile and remain in the engine diluting the oil. It is the blow-by gas that contaminates the oil and gives it that characteristic smell after only a few hours.
The blow-by components that remain in the oil are real troublemakers. They not only dilute the oil and additives but in the upper ring zone they overwhelm the dispersant and antioxidants leading to carbon and lead deposits. Analysis of deposits found in the upper piston ring groove show them to contain over 2% lead and therefore fuel derived. Oil companies only put enough antioxidant to protect the bulk oil from oxidizing. This however is not the problem. CamGuard uses multiple high molecular weight antioxidants to address this “blow-by fuel dilution” unique to aircraft engines. The result is fewer deposits, which dramatically reduces the chance of sticking piston rings or valve guide “morning sickness”.
High Pressure Differential Scanning Calorimetry (HPDSC) is used to directly measure an oils resistance to oxidation and tendency to form deposits. A small oil sample is placed in a high-pressure cell under150psi of oxygen, where it is heated to a temperature of 200° (392°F) and held constant. The time to the onset of oxidation in minutes, determined by the instrument by release of heat, indicates the oils stability. The longer the time the better.
We tested a popular 15W-50 semi-synthetic oil with and without the addition of 5% CamGuard. The results show a huge increase in the time to oxidation with the use of CamGuard. The substantial increase in oxidation stability when using CamGuard is very important in air-cooled aircraft engines as explained above.
ASL CamGuard Wear Testing
Aircraft Specialties Lubricants performed wear testing of four oils and three additives was performed utilizing a FALEX Tribometer at a third party analytical laboratory. The FALEX PIN and V-block is a well-known tribometer that is used for many standardized lubricant tests. These include the ASTM (American Society for testing and Materials)) D-2670 Standard Test Method for Measuring Wear Properties of Fluid Lubricants and ASTM D-3233 Standard Test Method for Measurement of Extreme Pressure (EP) Properties of Fluid Lubricants.
The test procedure utilized here was a derivative of the ASTM D-2670 and used by Phillips Petroleum and described in the Journal "WEAR" Volume 84, 1983. The Phillips test correlates well with camshaft wear in automotive engines using gasoline engine oils. The loads in this testing were then reduced from the above reference and specifically selected to demonstrate effectiveness of the antiwear additives in commercial aviation oils. Aircraft engines were designed before there were antiwear oil additives. The engines were designed with cam/ lifter and piston ring/ cylinder load pressures low enough that a film of heavy oil was enough to prevent excessive wear.
The test procedure consists of heating the test oil to 250 degrees F. and then with the pin rotating at 290 RPM slowly ramping up the load to 150 pounds and running for a three minutes break-in. The load was then stepped up to 250 pounds for 1 minute and then stepped up to 350 pounds. The total run time is 3.5 hours with a constant 350-pound load. The PIN and V- blocks are cleaned and the total weight loss is measured and reported.
Ashless additives such as the triaryl phosphate ester functional fluids including tricresyl phosphate (TCP), butylated triphenyl phosphate (BTPP), and isopropylated triphenyl phosphate have historically been utilized as load carrying, plasticizers and flame-retardant additives in many applications. They are currently utilized extensively in turbine engine oils. These additives have never demonstrated useful performance in automotive applications i.e., the engines wear out. Automotive gasoline and diesel engines depend on the use of zinc diakyldithiophosphate "zinc" for antiwear protection.
Like other bench tests, this is an accelerated test. The loads and initial temperatures of this test were specifically selected to test the antiwear capabilities of these oils and additives and not their extreme pressure (EP) properties, which occur at significantly higher loads. It is important to remember that even non-dispersant mineral oil passes the aviation certification test and consists only of basestock and antioxidant. The ashless dispersant (AD) non-antiwear additized oils have all successfully passed certification testing and it is important to note that this is a test to compare the antiwear additive chemistries under conditions just beyond those found in an engine. The test conditions were determined by using conditions that are just severe enough that the unadditized oils fail. Only after a great deal of testing under a wide variety of conditions was it determined that this procedure could be used to test the antiwear additive's effectiveness.
Figure 1 shows the results of tests at the selected conditions. The samples that did not make it up to the final load, 350 pounds, are shown as failing with the appropriate explanation. The samples that made it to the final load but did not run the full length of time, 3.5 hours, are shown as failing with the appropriate explanation. The W100 failed just before it reached the 350-pound final load and was chosen to be the base case for additive testing. The 20W-50 failed at 75 seconds but at a much lower starting temperature of 150 degrees F and could have been used as the base case as well.
The additized W100 Plus and the leading semi-synthetic (15W-50 SS) both of which claim antiwear protection performed well. The 15W-50 gave a total weight loss of 54.9mg and the W100 Plus gave a total weight loss of 28mg. The new 20W-50 SS, which makes antiwear claims, failed 15 seconds after reaching the final load and in 5 seconds in a repeat test. CamGuard was added to both of the semi synthetics the 15W-50 SS and 20W-50 SS and demonstrated excellent results with 6.1mg and 4 mg weight loss respectively also shown in Figure 1.
Additive A, a well know product, in W100 demonstrated no benefit over the W100 by itself as the sample failed to reach the final load. Additive B, a polymer resin type additive in the W100 sample made it to the final load but failed after 15 seconds. CamGuard in the reference W100 sample passed with a total weight loss of only 1.5-mg and are show in Figure 2.
ASL CamGuard Seal Conditioning
Most seals (gaskets) are elastomeric materials and are found throughout the engine. They keep the oil inside the engine while allowing mechanical motions to run through the engine from inside to outside i.e. the crankshaft and allow access to engine components.
Heat and time harden and shrink seals so that over the years oil weeping becomes a common occurrence. CamGuard nullifies these effects to keep seals supple and doing their job.
Certain additives, found in some commercial oils and additives, can break down and lead to seal degradation and need for premature seal replacement. See Figure 3. CamGuard mitigates this problem by blocking aggressive chemical attack.
Degraded seal due to commercial oil additive attack
Figure 3
ASL CamGuard Engine Oil Analysis
Here is the typical response of a lower time engine when starting on CamGuard.
In the above graph, the average of three analyses with 20W-50 semi-synthetic oil without CamGuard is shown in red. The average of two subsequent analyses of the same oil with CamGuard is shown in blue. There is a dramatic reduction in all metals when using CamGuard on a per hour basis. The + 10 % error bars are shown to reinforce the significant difference that is achieved with the use of CamGuard.